|
|
Nowa indukcyjnościowa metoda pomiaru masy
Wszystkie wagi firmy MENSOR oparte są na nowej indukcyjnościowej metodzie pomiaru masy oraz indukcyjnościowych belkach pomiarowych polskiej produkcji - nie importujemy belek tensometrycznych z Chin. Główne zalety ww. metody pomiarowej w stosunku do wag tensometrycznych są następujące:
-
wysoka odporność mechaniczna na przeciążenia - dla małych zakresów pomiarowych do 1000% - możliwe duże wymiary pomostów wagowych.
- wysoka dokładność wynikająca z mniejszych niż w przetwornikach tensometrycznych naprężeń wewnątrz belki pomiarowej - rozdzielczość 1mg
- małe gabaryty i wysoka odporność na przeciążenia, indukcyjnościowych belek pomiarowych
- wielokrotnie mniejszy ciężar własny wag indukcyjnościowych od analogicznych wag wyposażonych w siłowniki magnetoelektryczne
- belki indukcyjnościowe są wielokrotnie odporniejsze na boczne uderzenia od belek tensometrycznych
Powyższe zalety zostały sprawdzone
- w wyniku piętnastu lat produkcji wag indukcyjnościowych na rynek polski i niemiecki
- przez Główny Urząd Miar Certyfikat zatwierdzenia typu WE NR PL 06 003
- przez Polskie Centrum Badań i Certyfikacji Certyfikat zgodności CE Nr MD – 220/1/2009
- przez użytkowników wag Brązowy Laur Konsumenta 2005 rok

- indukcyjnościowy system pomiarowy został nominowany do nagrody w konkursie Polski Produkt Przyszłości 1998 rok (w kategorii wyrób przyszłości)
Prace badawcze nad indukcyjnościową metodą pomiaru masy były dofinansowane z środków Unii Europejskiej w ramach trzech krajowych projektów badawczych a obecnie kontynuowane są w ramach międzynarodowego projektu EUROSTARS E! 4637 – EXCALE.
Theoretical basis of inductive method for measure of mass (pdf ver. )

|
METROLOGY AND MEASUREMENT SYSTEMS
Index 330930, ISSN 0860-8229
www.metrology.pg.gda.pl |
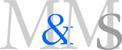
|
INDUKCYJNOŚCIOWY CZUJNIK POMIARU MASY |
Janusz Lewandowski
MENSOR |
|
Wstęp
Tensometryczne belki pomiarowe są powszechnie stosowane do budowy wag elektronicznych i modułów wagowych. Masowa produkcja tych elementów spowodowała osiągnięcie ich wysokiego poziomu konstrukcyjno technologicznego i niskich kosztów wytwarzania - opracowanie nowych rozwiązań konstrukcyjno technologicznych w tej dziedzinie jest zatem szczególnie trudne.
Wprowadzenie nowej zasady działania oraz wykorzystanie nowych zjawisk fizycznych wydaje się jedyną drogą dla postępu technologicznego w dziedzinie pomiarów masy. Tensometryczna belka pomiarowa składa się z dwóch elementów: belki sprężystej wykonanej najczęściej ze stopu aluminium lub stali nierdzewnej oraz czujników tensometrycznych.
Koncepcja belki sprężystej jako elementu pomiarowego, do którego zostaje przyłożona zewnętrzna siła mierzona jest słuszna, ponieważ stanowi ona stabilny, powtarzalny, odporny na przeciążenia zespół mechaniczny. Wątpliwości pojawiają się w stosunku do tensometrów, które naklejone na belkę mierzą naprężenia na jej powierzchni w najcieńszym przekroju.
Tensometr foliowy poddany siłą rozciągającym jest mało odpornym elementem pomiarowym głównie ze względu na fakt połączenia go z belką za pomocą kleju, który wraz z zewnętrznymi warstwami belki poddawany jest rozciąganiu lub ściskaniu. Ponad to, warstwa kleju usytuowana między belką a tensometrem ma wpływ na charakterystykę statyczną całego układu pomiarowego, co przy większych zakresach pomiarowych np. kilku kilogramów, posiada pomijalne znaczenie - natomiast dla małych zakresów pomiarowych wpływ sztywności kleju jest znaczący. Stąd praktyczną granicą stosowania belek tensometrycznych jest zakres pomiarowy od 0-200g a w większości zastosowań zakres od 0 do 2 kg - wagi elektroniczne o udźwigach poniżej ww. zakresów pomiarowych budowane są za pomocą przetworników magnetoelektrycznych.
Biorąc pod uwagę fakt, że własności sprężyste dobrych stopów aluminium i stali nierdzewnej pozwalają na budowę przetworników siły wykorzystujących jako zasadę działania pomiar tych własności, założono w prezentowanych tutaj badaniach tę zasadę jako niezmienną, tzn. założono, że siłę F przełożoną do końca belki pomiarowej mierzy się poprzez pomiar jej ugięcia x:
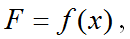
gdzie: F - mierzona siła (i masa), x – ugięcie końca belki
Zrezygnowano natomiast z pomiaru ugięcia x za pomocą tensometrów, zastępując je indukcyjnościowym czujnikiem przesunięcia. Tym bardziej, że czujniki tensometryczne mierzą ww. ugięcie x drogą pośrednią poprzez pomiar naprężeń na powierzchni belki. Tymczasem indukcyjnościowy czujnik przesunięcia jest powszechnie znanym dobrym czujnikiem do pomiaru małych przemieszczeń x.
Przyjęta zasada działania jest wyjątkowo prosta – niestety jej realizacja stwarza wiele problemów konstrukcyjno technologicznych. Do głównych problemów należy zaliczyć tutaj wpływ zmian temperatury otoczenia na uzwojenia indukcyjnościowego czujnika przesunięcia, który w tym przypadku stanowi rezystorowy czujnik temperatury. Podobnie temperatura otoczenia zmienia moduł Younga stopu aluminium z którego wykonany jest belka pomiarowa, co znacząco wpływa na jej własności sprężyste.
Osobnym problemem jest tutaj rozkład pola magnetycznego, powstającego wokół indukcyjnościowego czujnika przesunięcia, pole to inaczej przenika przez szczeliny powietrzne a inaczej przez stop aluminium tworząc w nim prądy wirowe. Ponad to rozkład pola magnetycznego może zostać zakłócony w wyniku wprowadzenia w jego obszar przedmiotu metalowego np. postawienie na szalce wagi wzorca masy.
Uzyskanie wysokiej rozdzielczości indukcyjnościowego czujnika przesunięcia oraz jego liniowej charakterystyki statycznej stanowi poważny problem konstrukcyjny. Stąd zastosowanie handlowych indukcyjnościowych czujników przesunięcia nie jest tutaj możliwe.
Podstawowe problemy konstrukcyjno technologiczne indukcyjnościowej belki pomiarowej związane są z usytuowaniem otworów i kanałów w jej wnętrzu - wiąże to się z wyborem optymalnej technologii obróbki skrawaniem oraz obróbką cieplną stopu aluminium.
Rozwiązanie powyższych problemów stanowi przedmiot niniejszej pracy, prowadzonej systematycznie w okresie kilkunastu lat przez wiele instytutów i uczelni politechnicznych, pod kierunkiem firmy badawczo produkcyjnej MENSOR. Należy podkreślić, że rezultaty poszczególnych wyników badań były testowane w krótkich seriach produkcyjnych wag elektronicznych oraz opiniowane przez ich użytkowników. Proces ten wielokrotnie powtarzany zapewniał systematyczne podwyższanie poziomu konstrukcyjno technologicznego indukcyjnościowych belek pomiarowych – bez powiązania procesów produkcyjnych z badaniami, osiągnięcie opisanych w niniejszej pracy rezultatów nie było by możliwe.
2. Stan techniki pomiarów masy
W technice pomiarów masy rozpowszechnione są dwa systemy pomiarowe.
Oparty na kompensacji w układzie równowagi sił, masy ważonej za pomocą siłownika magnetoelektrycznego (rys. 4-1) Masa ważona jest tutaj proporcjonalna do prądu płynącego przez cewkę:
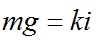
gdzie: m – masa ważona, g – przyspieszenie ziemskie, k – współczynnik proporcjonalności, i – prąd płynący przez cewkę
stąd:
(1)
(2)
W praktycznym rozwiązaniu pomiaru masy (rys. 4-1) siła mg przyłożona jest przez układ dźwigniowy o różnym przełożeniu zależnym od zakresu masy mierzonej. W przypadku wag górno szalkowych, potrzebny jest układ dźwigniowy kompensujący nie osiowe obciążenie szalki masą ważoną. Opisany układ pomiarowy jest powszechnie stosowany w przypadku dokładnych pomiarów masy i małych zakresów pomiarowych np. w wagach analitycznych.
Rys. 4-1. Schemat ideowy układu pomiaru masy za pomocą siłownika magnetoelektrycznego, 1- magnes stały, 2 – cewka zawieszona za pomocą układu dźwigniowego (niewidoczny na rysunku).
Ma on jednak wiele wad, do których należy zaliczyć:
- skomplikowana precyzyjna konstrukcja mechaniczna przełożenia dźwigniowego i mechanizmu kompensującego błąd nie osiowego przyłożenia siły
- dość duża masa wynikająca z wymiarów gabarytowych magnesu stałego (rys. 4-1)
- mała odporność na zewnętrzne zmienne pola magnetyczne
- znaczny pobór energii (prąd i - równanie (2)), któremu towarzyszy wydzielanie ciepła i zmiana temperatury panującej wewnątrz wagi
- mała odporność na wstrząsy, przyspieszenia i drgania
Wymienione niedogodności były powodem poszukiwania innych rozwiązań konstrukcyjnych pozbawionych ww. wad.
2. W latach sześćdziesiątych powstało nowe rozwiązanie konstrukcyjne oparte na pomiarze odkształceń sprężystych specjalnego profilu wykonanego ze stopu aluminium lub ze stali (rys. 4-2)
Rys. 4-2. Tensometryczna belka pomiarowa: 1- korpus belki, 2 - tensometry
Cztery tensometr naklejone w miejscach o najmniejszym przekroju zmieniają swoją rezystancję w wyniku obciążenia belki siłą mg. Połączone są one w układzie mostka Wheatstona, którego napięcie wyjściowe U proporcjonalne jest do masy mierzonej m.
(3)
gdzie: U – napięcie w przekątnej mostka, –proporcjonalności, m –masa mierzona.
Opisane rozwiązanie wprowadzało znaczny postęp w technice pomiarów masy; jest ono proste i bardziej niezawodne od systemu opartego na siłowniku magnetoelektrycznym; możliwy jest tutaj pomiar dużych mas przy małym poborze mocy. Rozwiązanie to znalazło powszechne zastosowanie w budowie wag elektronicznych, głównie o udźwigach powyżej dwóch kilogramów i rozdzielczości nieprzekraczającej 6000 działek.
Belka tensometryczna rys. 4-2 ma jednak również wiele wad:
- małą odporność na przeciążenia pionowe i boczne (150%)
- zakres zastosowań ograniczony do wag o udźwigach powyżej 2 kg (wykonywane są również wagi tensometryczne o zakresach pomiarowych poniżej 2 kg, ale mają niższą dokładność i nie spełniają normy PN-EN 45501)
- ograniczona dokładność pomiaru (na ogół wagi III klasy dokładności)
- skomplikowaną technologię naklejania tensometrów.
- konieczność kompensacji zmiany modułu Younga belki metalowej w funkcji temperatury przez odpowiedni dobór czujników tensometrycznych
Pomimo ww. wad belki tensometryczne znalazły obok układu w/g rys. 4-1 powszechne zastosowanie i wielu konstruktorom wag trudno sobie wyobrazić ich budowę bez tego zespołu pomiarowego.
3.Indukcyjnościowa belka pomiarowa
Nowe rozwiązanie konstrukcyjne prace [40], [41] wykorzystuje inne zjawiska fizyczne od wyżej opisanych. Zrezygnowano z tensometrów, które przeznaczone są z zasad swojej budowy do pomiaru miejscowych naprężeń w konstrukcjach metalowych – zastosowano natomiast znany w innych dziedzinach metrologii indukcyjnościowy czujnik przesunięcia (rys. 4-3)
Rys. 4-3. Schemat indukcyjnościowego czujnika przesunięcia: 1 – rdzeń ferrytowy, 2 – cewki, 3 – kubek ferrytowy, a, b, c – wyjścia z cewek
Składa się on z dwóch cewek przeciwnie nawiniętych, ruchomego rdzenia i kubka ferrytowego, przez który zamyka się zmienny strumień pola magnetycznego wytworzonego przez prąd płynący przez cewki. Omawiany czujnik pracuje w układzie różnicowym tzn. w środkowym symetrycznym położeniu rdzenia względem cewek napięcie wyjściowe układu pomiarowego (rys. 4-4) jest równe zero. Przesuniecie rdzenia względem tego stanu równowagi powoduje pojawienie się napięcia U proporcjonalnego do przesunięcia x rdzenia ferrytowego.
Rys. 4-4. Schemat mostka pomiarowego czujnika indukcyjnościowego, 1 – wzmacniacz prądu zmiennego, 2 – cewki, 3 – rezystory, U – napięcie wyjściowe z mostka
Rys. 4-5. Indukcyjnościowa belka pomiarowa, 1 – indukcyjnościowy czujnik przesunięcia, 2 – rdzeń czujnika, 3 – ruchoma część belki, 4 – stała część belki, 5, 6 - sprężyny pomiarowe.
Opisany wyżej indukcyjnościowy czujnik przesunięcia zastosowano do budowy indukcyjnościowej belki pomiarowej (rys. 4-5). Ruchoma część belki połączona jest z szalką wagi, na która nakładamy masę ważoną. W wyniku położenia tej masy następuje niewielkie ugięcie płaskich sprężyn oraz przemieszczenie rdzenia indukcyjnościowego czujnika przesunięcia. Rdzeń czujnika połączony jest z ruchomą częścią, zaś korpus indukcyjnościowego czujnika przesunięcia z częścią stałą indukcyjnościowej belki pomiarowej.
Elementami pomiarowymi indukcyjnościowej belki są dwie płaskie równoległe do siebie sprężyny, utwierdzone z jednej strony w stałej części belki z drugiej strony w części ruchomej. Ww. połączenia są trwałe, ponieważ sprężyny wykonane są z tego samego materiału, co część stała i ruchoma, metodą obróbki skrawaniem.
4. Porównanie belki tensometrycznej z indukcyjnościową
Pomiędzy belką tensometryczną (rys.4-6b) a indukcyjnościową (rys. 4-6a) istnieją następujące różnice:
- Pomiar ugięcia belki indukcyjnościowej jest bezdotykowy – układ sprężysty nie jest obciążony sztywnością tensometrów i kleju.
- Czujnik indukcyjnościowy mierzy całkowite, wypadkowe ugięcie belki pomiarowej, a tensometry mierzą odkształcenia sprężyste w określonych miejscach tej belki. W belce tensometrycznej ze względów technologicznych i produkcyjnych, konieczne jest spiętrzenia naprężeń w miejscach klejenia tensometrów. Odcinek (rys. 4-6), w którym następuje największe odkształcenie powierzchniowe musi być większy od czynnej długości tensometru, aby było można go nakleić w sposób powtarzalny na tę powierzchnię. Miejscowe spiętrzenie naprężeń, przybliża ich wartość do naprężeń dopuszczalnych dla danego materiału. Wpływa to na zwiększenie histerezy i wywołuje zjawisko „płynięcia” materiału pod stałym obciążeniem.
- Rdzeń czujnika indukcyjnościowego przesunięcia może się swobodnie przemieszczać nawet do 1 mm, co pozwala na uzyskanie w wagach o małych udźwigach 10-krotnego przeciążenia – ma to szczególne znaczenie w przemysłowych zastosowaniach wag elektronicznych, zbudowanych na omawianej belce indukcyjnościowej.
- Belka indukcyjnościowa może mieć małe zakresy pomiarowe np. 0 – 30g, które są nieosiągalne dla belek tensometrycznych. Możliwa jest tutaj budowa wag laboratoryjnych II klasy, które aktualnie można wykonać jedynie w oparciu o siłowniki magnetoelektryczne.
- Indukcyjnościowa metoda pomiaru masy nie stwarza ograniczeń dla dużych zakresów pomiarowych rzędu dziesiątek ton. Pomiar całkowitego odkształcenia belki pomiarowej czujnikiem indukcyjnościowym w przeciwieństwie do pomiaru miejscowych naprężeń tensometrami, pozwala na prostsze rozwiązania konstrukcyjne np. pomiar wydłużenia pręta metalowego rozciąganego dwoma osiowo przyłożonymi siłami stanowi prosty przykład zastosowania metody indukcyjnościowej dla dużych zakresów pomiarowych.
- Dokładność indukcyjnościowej belki pomiarowej jest wyższa niż belki tensometrycznej, co wynika z rozkładu naprężeń w obu belkach (rys. 4-6). Mniejsze naprężenia w sprężynach pomiarowych belki indukcyjnościowej zapewniają mniejszą histerezę, mniejsze płynięcie materiału pod stałym obciążeniem i większą liniowość charakterystyki statycznej.
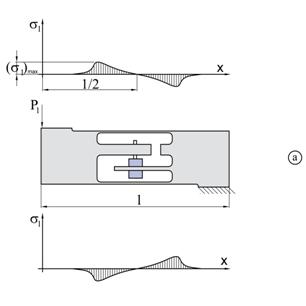
Fig. 4.6. Tension distribution of inductive load cell “a” and strain gauge load cell “b”.
Zakładając jednakowe obciążenie belki tensometrycznej i indukcyjnościowej rys. 4-6 siłami i rys. 4.6.
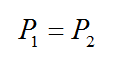
gdzie:  – przyłożona do belki indukcyjnościowej,  – siła przyłożona do belkitensometrycznej oraz przyjmując jednakowe ugięcia obu belek:  i:  :
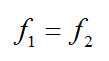
gdzie:  – ugięcie belki indukcyjnościowej,  – ugięcie belki tensometrycznej
Z twierdzenia Castigliana definiującego wewnętrzną energie sprężystą V obu belek, wytworzoną w wyniku przyłożenia sił zewnętrznych i mamy:
(4)
Z powyższych równań widać, że wewnętrzne energie sprężyste obu układów są jednakowe, zatem powinny być jednakowe pola pod krzywymi:
(5)
stąd uwzględniając charakter krzywych i maksymalne naprężenia w belce tensometrycznej są znacznie większe od maksymalnych naprężeń belki indukcyjnościowej przy założeniu jednakowych warunków zewnętrznych oraz tych samych materiałów z których są wykonane obie belki:
(6)
Zatem wykonując dwie belki: tensometryczną i indukcyjnościową z tego samego materiału, błędy histerezy i pełzanie pierwszej z nich będą mniejsze.
Obliczenie charakterystyki statycznej belki indukcyjnościowej jest stosunkowo proste, strzałka jej ugięcia może być wyznaczona ze znanego w wytrzymałości materiałów równania:
(7)
gdzie: l – długość sprężyn, – siła, b – szerokość sprężyn, h – grubość sprężyn, E – moduł Younga.
5. Korekta błędów mechanicznych belki metodą cyfrową
Główne prace badawcze nad indukcyjnościową belką pomiarową dotyczą podwyższenia jej własności metrologicznych na drodze mechanicznej tj. doborem optymalnej geometrii, zastosowaniem odpowiednich materiałów, optymalizacją technologii wytwarzania itd. Element mechaniczny, który posiada dobre własności metrologiczne jest bardziej niezawodny i tańszy w produkcji od zespołu pomiarowego wyposażonego dodatkowo w układ elektroniczny.
Niestety, istnieje granica możliwości podwyższania własności metrologicznych belki indukcyjnościowej na drodze mechanicznej – pozostaje wówczas zastosowanie techniki cyfrowej. Rzeczywista wartość sygnału wyjściowego belki pomiarowej wprowadzona jest wówczas do pamięci procesora, a następnie korygowana odpowiednim dla danego rodzaju błędów równaniem matematycznym. Opracowanie algorytmu korekty błędów oraz zaprojektowanie odpowiedniego równania, stanowi pierwszy ważny etap procesu programowania.
Przed przystąpieniem do omówienia ww. metod cyfrowej korekty błędów mechanicznych belki indukcyjnościowej należy przeprowadzić analizę zjawisk fizycznych, które powodują te błędy.
5.1. Histereza
Indukcyjnościowa metoda pomiaru masy opiera się na pomiarze ugięcia belki sprężystej, która jak każdy element sprężysty charakteryzuje się histerezą. Wartość tej histerezy dla belek wykonanych ze stopu aluminium PA6 lub PA7 jest bardzo mała i wynosi przeciętnie 3 do 5 działek przy rozdzielczości 30 000. Wyniki badań histerezy belki o udźwigu 15kg przedstawia tabela rys. 4-7. (do badań histerezy stosowano również elektroniczny układ pomiarowy o rozdzielczości 100 000 za pomocą, którego stwierdzono, że błędy histerezy układu elektronicznego o rozdzielczości 30 000 stosowanego do budowy wag elektronicznych są pomijalnie małe w stosunku do analogicznych błędów mechanicznych belki indukcyjnościowej).
m [kg] |
wskazanie (narastająco)
[kg] |
wskazanie (malejąco)
[kg] |
0,05 |
0,0495 |
0,0500 |
0,5 |
0,4995 |
0,5005 |
2 |
1,9995 |
2,0010 |
5 |
4,9995 |
5,0010 |
10 |
10,0000 |
10,0005 |
15 |
14,9990 |
14,9990 |
Rys. 4-7 Tabela wyników badań histerezy belki indukcyjnościowej o udźwigu 15kg do Rys. 4-8
Ww. tabela przedstawia wartości masy m, jaką była obciążana belka w funkcji wskazań w wyświetlacza modułu wagowego dla narastających i malejących wartości m:
m = f(w)
gdzie: m – masa, którą była obciążana belka, w – wskazania wyświetlacza.
(8)
where: m – the mass loading the beam, w – indication of display.
Powyższe wyniki badań można przedstawić w postaci wykresu, gdzie na osi rzędnych podana jest różnica między teoretyczną prostą o nachyleniu . wyznaczona przez połączenie początku układu współrzędnych z punktem leżącym w odległości ¾od początku tego układu, rys. 4-8.
Rys. 4-8 Wykres błędów histerezy belki indukcyjnościowej o udźwigu 15kg
Z uwagi na małe wartości błędów histerezy indukcyjnościowej belki pomiarowej na osi odciętych rys. 4-8 zastosowano 1000 krotne powiększenie w celu ilustracji typowej pętli histerezy. Małe wartości błędów histerezy, jakimi charakteryzują się stopy aluminium typu PA6 stanowią szczególnie korzystną cechę przy ich zastosowaniu do budowy układów pomiarowych.
Wartość histerezy belki indukcyjnościowej zależy od dwóch parametrów:
- geometrii sprężyn pomiarowych
- rodzaju materiału, z którego wykonano belkę
Zgodnie z rozdziałem 4.1 małą histerezą charakteryzują się belki posiadając płaskie sprężyny pomiarowe. Wykonanie jednak tych sprężyn podobnie jak w belkach tensometrycznych tj, w postaci otworów usytuowanych w pobliżu zewnętrznych powierzchni belki rys. 4-9 powoduje błędy histerezy dopuszczalne dla wag III klasy.
Rys. 4-9 Kołowy kształt sprężyny pomiarowej
Technologia wykonania sprężyny pomiarowej pokazanej na rys.4-9 jest oczywiście prostsza od technologii wykonania sprężyny płaskiej. Pomimo podobnego kształtu w tym przypadku, sprężyny pomiarowej belki indukcyjnościowej i tensometrycznej zasada działania obu belek oraz warunki pracy sprężyny są różne. W przypadku belki tensometrycznej mierzymy naprężenia na powierzchni najmniejszego przewężenia przekroju, natomiast w belce indukcyjnościowej mierzymy sumaryczne, całkowite ugięcie czterech sprężyn.
Dodatkowym czynnikiem wpływającym na wartość omawianej histerezy jest obróbka skrawaniem stosowana przy wykonywaniu indukcyjnościowej belki pomiarowej. Podczas tej obróbki wydziela się ciepło, które wpływa na zmianę struktury krystalicznej warstwy materiału znajdującej się w pobliżu narzędzia skrawającego, pogarszając jego własności sprężyste.
Sumaryczny efekt tego zjawiska jest tym większy im cieńsza jest sprężyna pomiarowa, ponieważ uszkodzona w wyniku skrawania warstwa materiału stanowi większy, procentowy udział w całej grubości sprężyny. Z drugiej strony w cieńszych sprężynach występują znacznie mniejsze naprężenia od dopuszczalnych dla danego materiału. Nakładające się na siebie ww. zjawiska powodują, że w praktycznych rozwiązaniach konstrukcyjnych indukcyjnościowych belek pomiarowych najmniejsza histereza występuje dla zakresów pomiarowych leżących w pobliżu 0-15kg, rys. 4-10.
Rys. 4-10 Wartość histerezy belki indukcyjnościowej w funkcji zakresów pomiarowych - jako wynik obróbki skrawaniem i naprężeń występujących wewnątrz sprężyn pomiarowych
5.2. Pełzanie materiału belki pod stałym obciążeniem
Zjawisko pełzania materiału pod stały obciążeniem jest powszechnie znane w wytrzymałości materiałów – występuje ono również w przypadku indukcyjnościowej belki pomiarowej. Podobnie jak w przypadku histerezy powolny wzrost ugięcia belki indukcyjnościowej obciążonej stałą siłą zależy od:
- rodzaju materiału
- geometrii belki
Charakterystykę uginania się belki w funkcji czasu pod wpływem obciążenia jej stałą siłą przedstawia rys. 4-11 – wykres czerwony.
Rys. 4-11 Charakterystyka belki indukcyjnościowej obciążonej masą m=15kg.
Z rys. 4-11 widać, że w pierwszych minutach po przyłożeniu obciążenia odkształcenia belki są stosunkowo szybkie – później omawiane odkształcenia maleją - w przybliżeniu w/g krzywej wykładniczej:
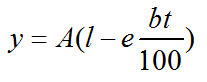
gdzie: y – ugięcie belki, A i b – współczynniki, t – czas.
(9)
Na rys. 4-11 narysowano krzywą wykładniczą (niebieska) wyznaczoną z ostatniego równania, dobierając tak współczynniki A i b aby obie krzywe się pokrywały.
W niektórych przypadkach lepsze przybliżenie charakterystyki pełzania otrzymuje się stosując dwa człony funkcji wykładniczej, ponieważ początkowe odkształcenie belki po obciążeniu ją masą jest stosunkowo szybkie a później zbliża się asymptotyczne do stałej wartości
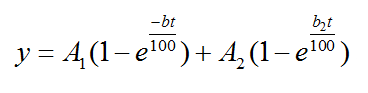
gdzie : y – ugięcie belki, t – czas, 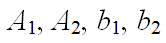 – współczynniki charakterystyczne dla danego rodzaju materiału
(10)
W celu wprowadzenia do programu wagi korekty zjawiska pełzania materiału indukcyjnościowej belki pomiarowej, należy współczynniki wyznaczyć doświadczalnie.
Zjawiska histerezy i pełzania są z sobą ściśle związane, pętla histerezy widoczna na rys. 4-8 powstaje w wyniku pełzania materiału dla poszczególnych punktów pomiarowych. Stąd wartości wskazań w leżące na dolnej krzywej są mniejsze od wartości wskazań leżących na prostej teoretycznej.
6. Wpływ temperatury otoczenia
Zmiana temperatury otoczenia wpływa na zmianę modułu Younga stopu aluminium, z którego wykonana jest indukcyjnościowa belka pomiarowa – powoduje to zmianę nachylenia charakterystyki statycznej (zmianę wzmocnienia) oraz przesunięcie początkowego punktu pracy. Równanie tej charakterystyki czyli równanie prostej w układzie współrzędnych (w, m) ma postać:
w = a·m+c
(11)
gdzie: w – wskazanie układu pomiarowego, m – masa ważona, a, c – współczynniki.

gdzie: T – temperatura otoczenia.
Współczynnik a określa wzmocnienie układu pomiarowego natomiast współczynnik c charakteryzuje przesunięcie omawianej charakterystyki na płaszczyźnie (m, w).
Na rys. 4-12 przedstawiono dwie charakterystyki statyczne: 1 – przed kompensacją temperaturową (czerwona), wyznaczoną po zmontowani wagi i 2 (niebieska) – po kompensacji temperaturowej tj. po zmianie współczynnika kompensującego zmianę wzmocnienia a oraz przy zmianie współczynnika c kompensującego przesunięcie punktu pracy.
Kompensacja temperaturowa wykonana jest przez przeprowadzenie prostej 2 przez dwa punkty dla obciążenia równego zero i obciążenia równego masie kalibracyjnej rys. 4-12.
Podczas normalnej pracy wagi temperatura otoczenia mierzona jest za pomocą czujnika temperatury z rozdzielczością ¼°C, a zmiana modułu Younga belki indukcyjnościowej korygowana za pomocą mikrokontrolera. Czujnik temperatury umieszczony jest w korpusie belki w celu zachowania tej samej dynamiki pomiaru, jaką posiada belka.
Rys. 4-12 Wpływ temperatury otoczenia na charakterystykę statyczną przetwornika indukcyjnościowego oraz kompensacja temperaturowa
7. Uwagi końcowe
Minimalizacja omówionych wyżej błędów wskazań indukcyjnościowej belki pomiarowej odbywa się w dwóch etapach:
- pierwszy etap obejmuje prace konstrukcyjno technologiczne prowadzone równolegle z produkcją seryjną np. minimalizację zjawiska histerezy i pełzania można uzyskać drogą doboru materiału z którego wykonana jest belka oraz za pomocą odpowiedniej obróbki cieplnej
- drugi etap dotyczy korekty błędów mechanicznych belki metodą cyfrową za pomocą odpowiednio oprogramowanego mikrokontrolera
Z punktu widzenia niezawodności działania wagi lepsze jest posiadanie takiej belki pomiarowej, która nie wymagała by dodatkowej kompensacji cyfrowej – można to osiągnąć dla wag III klasy. W przypadku wag II klasy konieczna jest już cyfrowa kompensacja omówionych wyżej błędów wskazań, szczególnie minimalizacja zjawiska: histerezy, pełzania materiału pod stałym obciążeniem i nieliniowości charakterystyki statycznej.
Wspólna konstrukcja indukcyjnościowych belek dla różnych zakresów pomiarowych pozwala na zastosowanie jednego typu mikroprocesora i jednego programu dla wszystkich rozwiązań konstrukcyjnych. Możliwe to jest dzięki identycznym błędom: histerezy, pełzania, liniowości charakterystyki statycznej, wpływu temperatury otoczenia i wilgotności dla zakresów pomiarowych od 20g do 400kg.
Wynika to z faktu, że wszystkie belki pomiarowe wykonane są z tego samego materiału, wyposażone w ten sam indukcyjnościowy czujnik przesunięcia oraz pracują przy tym samym ugięciu 0,2mm. Stąd przykładowo, wpływ zmian temperatury otoczenia na zmianę modułu Younga stopu aluminium z którego wykonane są belki pomiarowe jest identyczny dla wszystkich rozwiązań konstrukcyjnych.
Przedstawione w pracy wyniki badań były wykorzystane w produkcji indukcyjnościowych belek pomiarowych przez firmę MENSOR a wagi elektroniczne zbudowane na tych belkach uzyskały zatwierdzenie typu WE zgodne z normą Unii Europejskiej PN-EN 45501, nr PL 06 003 Wydane przez Główny Urząd Miar w Warszawie.
Literatura
- M. Jafaripanach, B.M. Al.-Hashimi, N.M. White: “Load Cell Response Correction using Analog Adaptive Techniques”. IEEE International Symposium on Circuits and Systems, Bangkok, Tailand, 2003, pp. IV752-IV755.
- M. Jafaripanach, B.M. Al.-Hashimi, N.M. White: “Dynamic Sensor Compensation Using Analogue Adaptive Filter Compatible with Digital Technology”. Accepted for publication in IEE Proc. Circuits, Devices & Systems.
- J. Lewandowski: Measuring Transmitter of Electronic Scales. Patent, no. PL 175320 B1.
- J. Lewandowski: “Computing Measuring System of Mass and Non-electric Physical Parameters”. Proceedings of the 3th International Seminar in Precision and Electronic Technology, INSEL 2007, Warsaw 19-20 Nov., vol. 3, 2007, pp. 187-190.
- J. Lewandowski: “Inductive Method for Measure of Mass”. PAR, no. 5, 2000. (in Polish)
- J. Lewandowski: “Inductive Sensors of Force”. Proceedings of the 4th International Seminar in Precision and Electronic Technology, INSEL 99, Warsaw 22-24 Nov., vol. 4,1999, pp. 225-231.
- TECH NOT Measurements Group – Fatigue Characteristics of Micro-Measurements Strain Gages, Measurements Group, Inc, P.O. Box 27777, Raleigh, North Carolina, USA.
- TECH NOT Measurements Group – Noise Control in Gage Measurements, Measurements Group, Inc, P.O. Box 27777, Raleigh, North Carolina, USA.
- TECH NOT Measurements Group – Errors Due to Transverse Sensitivity in Strain Gages, Measurements Group, Inc, P.O. Box 27777, Raleigh, North Carolina, USA.
Spis treści
Informacja o firmie MENSOR
Nowa indukcyjnościowa metoda pomiaru masy
Indukcyjnościowe belki pomiarowe
Wagi medyczne, wagi lekarskie
Wagi do ważenia zwierząt - weterynaryjne
Wagi platformowe, magazynowe
Wagi pomostowe, stołowe
Wagi i systemy liczenia elementów
Wagi hakowe
Wagi precyzyjne
Wagi laboratoryjne
Wagi dla automatyzacji produkcji
Sygnalizacja i dozowanie
Moduły wagowe
|
|